Peck Building Parking Garage Gets Facelift
Traffic Membrane and Concrete Repair
About Peck Building Parking Garage
The Peck Building Parking Garage was a unique project because of its location adjacent to the L.L. Bean facility. Hascall & Hall had to be mindful of the L.L. Bean employees’ needs as well as the needs of the building itself.
It’s most cost effective to make exterior masonry and concrete repairs during the spring and summer in New England. Even then, close attention must be paid to the ever-changing New England weather to ensure optimum performance of the products chosen for repair.
At Hascall & Hall we love our work, and it shows
We pride ourselves in the creativity, flexibility, ingenuity, experience, and superior workmanship we apply to each and every one of the projects we undertake. Browse through our gallery of projects representing an extensive body of work spanning over six decades. Then contact us at 1-800-464-1481 for a free consultation, or to speak with one our flooring contractors or restoration experts. Let us give your project the attention and know-how it deserves.
Location: Lewiston, Maine
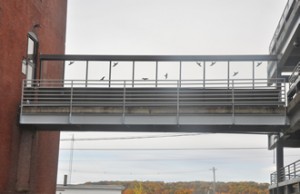